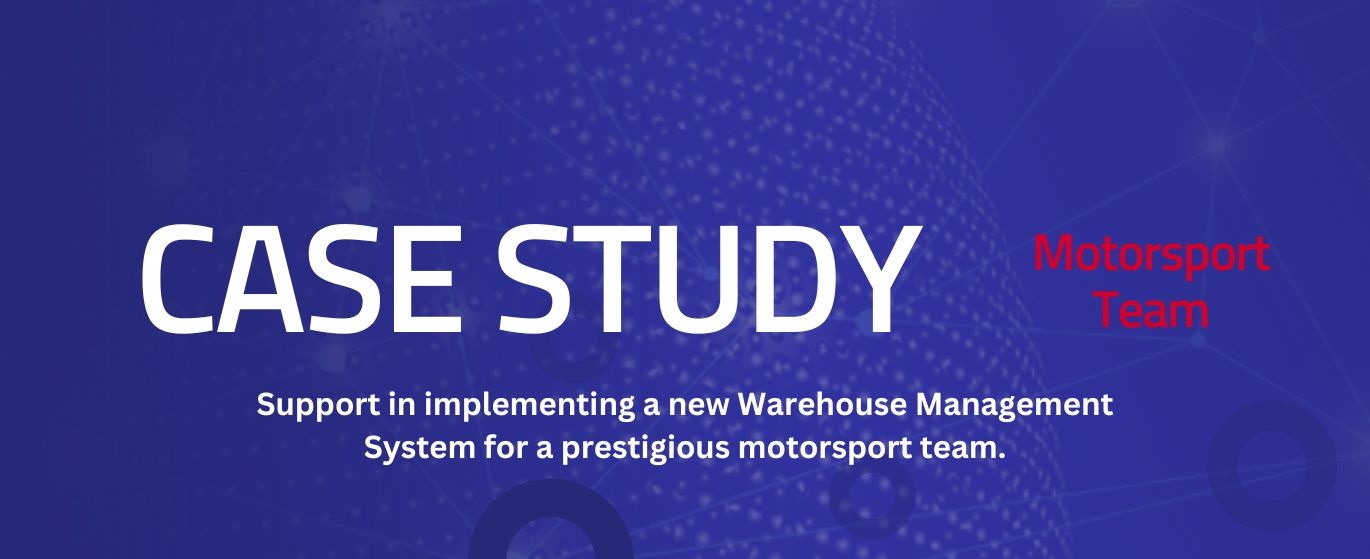
CASE STUDY
Market Sector : Supply Chain
Motorsport Team – warehouse stock management
Background
A well-known motor sport team faced significant challenges within their warehouse/storeroom due to an inefficient Warehouse Management System (WMS). The WMS could not keep up with the numerous daily demands, made by different departments both on and off-site. This led to incorrect data being inputted into the system. Orridge Supply Chain Services were engaged to support the team in tracking car parts from the racetrack to the warehouse.
What was required?
- Conduct constant PI (Perpetual Inventory) cycle checks five days a week within the storeroom and warehouse.
- Perform three stocktakes throughout the year to support the new WMS and correct any inaccurate inventory.
- Deploy skilled auditors to assess the actual level of discrepancies.
- Carry out delivery audits with the “Heritage Car” race team when race cars returned from overseas tracks.
Solution
Orridge SCS swiftly evaluated the full requirements of the project and developed an appropriate solution:
- Planned and executed numerous stocktakes in the warehouse and storeroom at the start of the year, deploying an appropriate number of auditors for the task.
- Post-count discrepancies were assessed after the stocktake with the stores team.
- Provided colleagues to conduct PI audits throughout the year.
- Arranged for colleagues to carry out “heritage car” site audits of car parts from retired race cars returning from sponsor weekends.
The outcome
The client was extremely satisfied with the speed, efficiency, and cost-effectiveness of the Orridge team. They were particularly impressed with how quickly Orridge SCS was able to assess, develop, and mobilise the necessary colleagues.
Key achievements
- Improved Accuracy: The new WMS, supported by regular PI cycle checks and stock takes, significantly improved the accuracy of inventory data. This led to better decision-making and reduced errors in the warehouse.
- Enhanced Tracking: The delivery audits ensured that car parts were accurately tracked from the racetrack to the warehouse, minimizing the risk of lost or misplaced items.
- Operational Efficiency: The deployment of skilled auditors and the systematic approach to audits streamlined warehouse operations, reducing downtime and increasing overall efficiency.
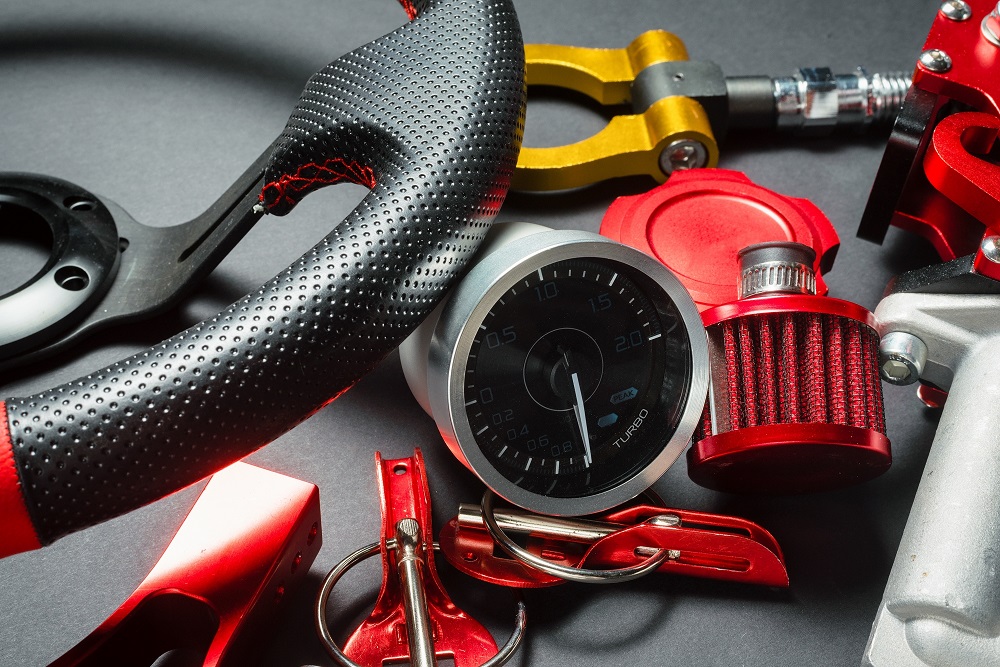
Other Related Case Studies
Our Service Sectors
Pharmacy Stocktaking
We specialise in all areas of healthcare from doctors’ surgeries, hospitals and other medical service providers.
FIND OUT MORERetail Stocktaking
Using your retail requirements as a foundation, Orridge harness our operational and technical expertise to deliver a bespoke package that will exceed your initial vision.
FIND OUT MORESupply Chain Auditing
Orridge are the specialist providers of supply chain management and stock auditing solutions, helping you maximise the effectiveness of these processes while also reducing time and expenditure.
FIND OUT MORE